The sprężarka śrubowa został wynaleziony przez Alfa Lysholma, profesora Królewskiego Szwedzkiego Instytutu Technologicznego, w 1934 roku. Jego pierwotnym zamierzeniem było doładowanie silników wysokoprężnych i turbin gazowych. Według odpowiednich statystyk: w ciągu 3000 godzin pracy awaria zespołu tłokowego jest 10 razy większa niż w przypadku zespołu śrubowego; w ciągu 12 000 godzin pracy awaria zespołu tłokowego jest 4 razy większa niż w przypadku zespołu śrubowego. Maszyna śrubowa jest typu obrotowego, a jej amplituda wynosi 1/5 amplitudy maszyny tłokowej, więc wibracje i hałas są stosunkowo niewielkie. Obecnie sprężarki śrubowe z wtryskiem oleju stały się głównymi modelami w dziedzinie aerodynamiki, chłodnictwa i klimatyzacji. W urządzeniu aerodynamicznym o średnim przepływie i urządzeniu chłodniczym o średniej wydajności chłodniczej zajmuje dominujący udział w rynku. W przemyśle spożywczym, medycznym i innych gałęziach przemysłu bezolejowe sprężarki śrubowe są wysoko cenione jako nowatorskie, czyste i wydajne sprężarki procesowe.
Główną częścią sprężarki śrubowej jest wirnik śrubowy. Zaawansowany charakter profilu wirnika determinuje wydajność całej maszyny, a wymagania dotyczące dokładności obróbki i obróbki cieplnej powierzchni są bardzo wysokie. Możliwość obróbki najbardziej zaawansowanej linii formierskiej stała się symbolem pomiaru siły ekonomicznej i siły technicznej przedsiębiorstwa zajmującego się obróbką. Obecnie profil wirnika został opracowany do trzeciej generacji - profil asymetryczny, obejmujący głównie niemiecki profil GHH, japoński profil Hitachi i szwedzki profil Atlas Copco SAP, wykorzystujący od 5 do 6 asymetrycznych profili zębów. Sprzęt do obróbki śrub oraz sprzęt pomiarowy i testujący są w zasadzie importowane z zagranicy, głównie z brytyjskiego centrum obróbczego HOLROYD, niemieckiego MAUSER, włoskiego DEA, brytyjskiego trójwspółrzędnego systemu pomiarowego IMS, ale ceny są bardzo drogie, często dziesiątki milionów juanów, a zwykłych przedsiębiorstw nie stać na zakup i rutynową konserwację, dlatego niektórzy krajowi producenci agregatów chłodniczych mają dwie możliwości produkcji lub dostawy: jedna to „sprowadzanie”, to znaczy sprężarki lub części głowic maszyn są kupowane bezpośrednio od zagranicznych profesjonalnych producentów. Obecnie do międzynarodowych marek sprężarek stosunkowo wysokiej jakości zaliczają się tajwańskie HANBELL, Fusheng, niemieckie BITZER, Grasso, włoskie REFCOMP, Fujihao, COMA, japońskie Hitachi, Daikin, Mitsubishi Heavy Industries, Kobelco, FRICK ze Stanów Zjednoczonych, Atlas Copco ze Szwecji ; Parowniki, skraplacze, odtłuszczacze itp. są przetwarzane w kraju, a niektóre importowane elementy sterowania elektrycznego (takie jak przemysłowe programowalne sterowniki PLC, programowalne ekrany dotykowe terminali, filtry, zawory rozprężne itp.) są montowane i wysyłane. . Drugi to „samodzielność”, to znaczy, z wyjątkiem elementów sterowania elektrycznego, wszystkie elementy głowicy maszyny, parowniki i skraplacze są przetwarzane i produkowane samodzielnie. Skala przedsiębiorstwa jest na ogół stosunkowo duża, a cały sprzęt do odlewania, przetwarzania i testowania jest importowany.
Aby zapewnić normalną, bezpieczną i niezawodną pracę sprężarki, należy zadbać o to, aby inne elementy urządzenia, w tym skraplacz, parownik, zawór dławiący lub rozprężny, działały normalnie, wymagany jest także szereg elementów sterujących do kontroli parametrów temperatury i ciśnienia podczas pracy sprężarki. Wykrywanie i przesyłanie informacji zwrotnych w czasie rzeczywistym oraz normalna praca całej maszyny jest koordynowana przez przemysłowy sterownik programowalny. Te automatyczne funkcje zabezpieczające muszą obejmować zabezpieczenie przed wysokim i niskim napięciem, zabezpieczenie poziomu oleju, zabezpieczenie przed przegrzaniem spalin, przegrzanie silnika i zabezpieczenie nadprądowe, utratę fazy i zabezpieczenie przed odwróceniem fazy. , zabezpieczenie przed odcięciem wody, zabezpieczenie przed zamarzaniem itp., aby automatycznie zatrzymać system, zablokować usterkę, wyświetlić informację o alarmie/ostrzeżeniu i wydać sygnał alarmowy w przypadku nieprawidłowości w systemie.
Agregaty chłodnicze są na ogół urządzeniami zużywającymi dużo energii, a ich wymagania dotyczące oszczędzania energii podczas pracy są bardzo ważne. Wymagane jest, aby urządzenie mogło automatycznie dostosowywać stan pracy do zmian obciążenia zewnętrznego, aby zapewnić pracę urządzenia pod optymalnym obciążeniem. Jednocześnie jednostka musi wykazywać się wydajnością przy częściowym obciążeniu, to znaczy może efektywnie pracować przy niższym obciążeniu i przy niskiej temperaturze wody w wieży chłodniczej oraz realizować regulację bezstopniową. Naturalnie, im szerszy zakres regulacji energii, tym lepiej. Przy projektowaniu układów chłodniczych często stosuje się ekonomiczne ekonomizery, aby część ciekłego czynnika chłodniczego przeszła przez chłodzenie pośrednie, aby poprawić stopień przechłodzenia, poprawiając w ten sposób wydajność chłodniczą na jednostkę czynnika roboczego. Jeśli chodzi o pomiar zużycia energii urządzenia, ważnym parametrem jest wydajność chłodnicza na jednostkę mocy wejściowej, a wyrafinowany sprzęt może osiągnąć ponad 4,5 W/W, co jest również znane jako współczynnik efektywności energetycznej lub współczynnik wydajności. wyrażony jako COP (współczynnik wydajności).
Przyjazny interfejs człowiek-maszyna jest również istotną częścią dobrze wykonanej jednostki chłodniczej. Generalnie wymagane jest użycie przemysłowego programowalnego sterownika z ekranem dotykowym i pełnym chińskim interfejsem. Ten tryb kombinowany jest prosty i łatwy do zrozumienia, ma silne właściwości przeciwzakłóceniowe i wysoki stopień automatyzacji. Operatorzy mogą swobodnie zmieniać ustawienia parametrów zgodnie z rzeczywistymi potrzebami produkcyjnymi i mają wiele funkcji, takich jak „wyświetlanie stanu pracy”, „wyświetlanie przyczyny awarii”, „wyświetlanie skumulowanego czasu pracy” itp. Dostarczone informacje o danych są kompletne i szczegółowe, co jest wygodne w przypadku zapytań historycznych i konserwacji
.
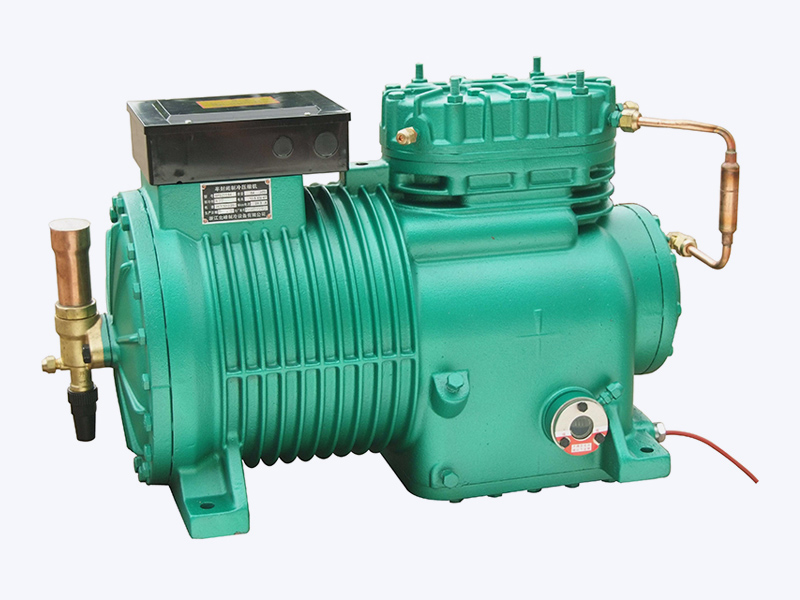